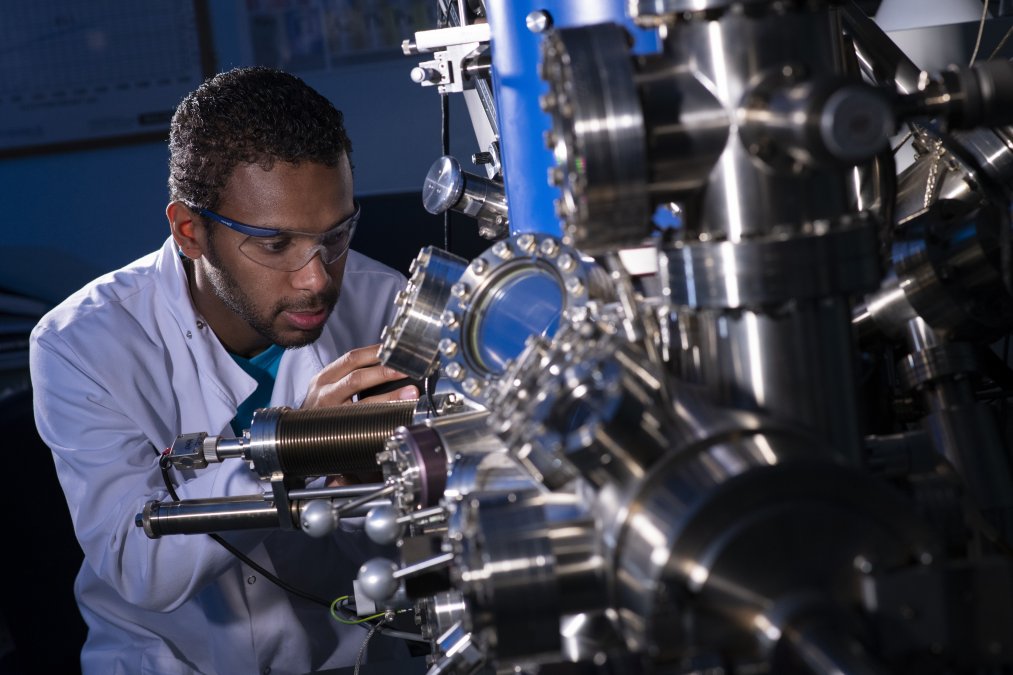
Despite the many benefits that lean manufacturing brings, companies often face difficulties in implementing this strategy. It is crucial that companies create a comprehensive plan to overcome any obstacles. Companies that have used Lean have discovered that there are three major issues that can hinder the success of the initiative.
Whatever the company's size, it is essential that they are committed to lean manufacturing. While there is no hard and fast rule to determine how committed a company is to the implementation of lean, it is important that management acquaints staff with the changes in the corporate culture.
It is also important to ensure that resources are allocated correctly. Many public organizations have found that they are wasting allocated budgets on items that are not necessary. Managers have been reported to buy equipment they don't need in order to save money. This can lead to operational bottlenecks and inefficient implementation of lean manufacturing.
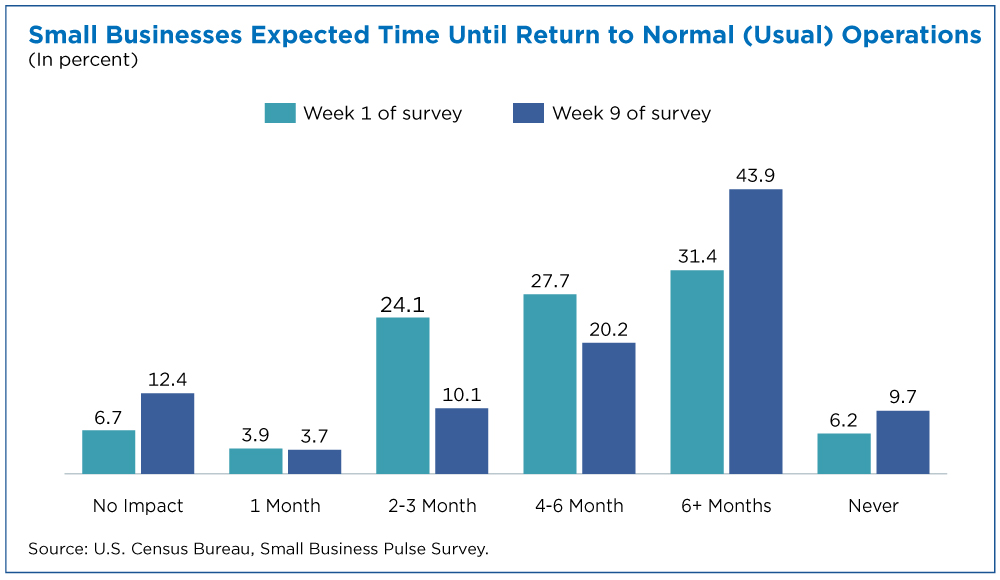
Resistance to cultural change is one the greatest obstacles to lean manufacturing. Many employees, especially those that have been with the company for a long time, are not comfortable with change. Some of these employees may be reluctant to accept change, even if the majority supports it. To break down resistance, managers must clearly communicate the benefits and justify the need for change.
Another significant challenge is the lack of a strategic transformation plan. While companies usually transform several business operations at once, it is important to maintain a long-term strategy. Companies can use this strategy to mentor and identify future leaders, improve their operations, and ensure that they remain competitive in the face technological advances. It helps identify operational bottlenecks and addresses growth opportunities.
This is not all. Training is essential to overcome resistance. A proper training program helps workers understand what their responsibilities are and what they can expect. This training helps workers acquire multi skills that can be used to help them work independently. Worker training also aids in problem solving, which allows them to maintain Lean through increased performance.
Management should engage with workers regularly to overcome resistance. Managers may try to force workers to follow their instructions but they must also explain why it is necessary. Ineffective implementation can be caused by managers who gave workers wrong instructions.
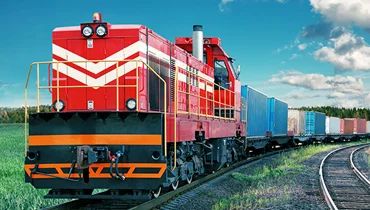
Regardless of the size of he company, managers must be involved on the shop floor, allowing them to identify the areas where changes can be made. They should also design and implement structured training programs for staff, as well as introduce digital tools to their work environment. These tools such as 5S improve visual management.
It is crucial to communicate and develop a clear vision of how lean manufacturing will be implemented. This vision should include the responsibilities of employees, a schedule for implementing lean, and a method for measuring success.
FAQ
Why is logistics important in manufacturing?
Logistics is an integral part of every business. Logistics can help you achieve amazing results by helping to manage product flow from raw materials to finished products.
Logistics play a key role in reducing expenses and increasing efficiency.
What are the four types in manufacturing?
Manufacturing is the process of transforming raw materials into useful products using machines and processes. Manufacturing involves many activities, including designing, building, testing and packaging, shipping, selling, service, and so on.
What does it take for a logistics enterprise to succeed?
To run a successful logistics company, you need a lot knowledge and skills. Effective communication skills are necessary to work with suppliers and clients. It is important to be able to analyse data and draw conclusions. You need to be able work under pressure and manage stressful situations. To increase efficiency and creativity, you need to be creative. You will need strong leadership skills to motivate and direct your team members towards achieving their organizational goals.
To meet tight deadlines, you must also be efficient and organized.
Statistics
- According to the United Nations Industrial Development Organization (UNIDO), China is the top manufacturer worldwide by 2019 output, producing 28.7% of the total global manufacturing output, followed by the United States, Japan, Germany, and India.[52][53] (en.wikipedia.org)
- Job #1 is delivering the ordered product according to specifications: color, size, brand, and quantity. (netsuite.com)
- According to a Statista study, U.S. businesses spent $1.63 trillion on logistics in 2019, moving goods from origin to end user through various supply chain network segments. (netsuite.com)
- You can multiply the result by 100 to get the total percent of monthly overhead. (investopedia.com)
- In 2021, an estimated 12.1 million Americans work in the manufacturing sector.6 (investopedia.com)
External Links
How To
How to Use Lean Manufacturing for the Production of Goods
Lean manufacturing (or lean manufacturing) is a style of management that aims to increase efficiency, reduce waste and improve performance through continuous improvement. It was developed by Taiichi Okono in Japan, during the 1970s & 1980s. TPS founder Kanji Takoda awarded him the Toyota Production System Award (TPS). Michael L. Watkins published the first book on lean manufacturing in 1990.
Lean manufacturing, often described as a set and practice of principles, is aimed at improving the quality, speed, cost, and efficiency of products, services, and other activities. It is about eliminating defects and waste from all stages of the value stream. Lean manufacturing is called just-in-time (JIT), zero defect, total productive maintenance (TPM), or 5S. Lean manufacturing focuses on eliminating non-value-added activities such as rework, inspection, and waiting.
Lean manufacturing can help companies improve their product quality and reduce costs. Additionally, it helps them achieve their goals more quickly and reduces employee turnover. Lean manufacturing is considered one of the most effective ways to manage the entire value chain, including suppliers, customers, distributors, retailers, and employees. Lean manufacturing is widely practiced in many industries around the world. Toyota's philosophy, for example, is what has enabled it to be successful in electronics, automobiles, medical devices, healthcare and chemical engineering as well as paper and food.
Five principles are the basis of lean manufacturing:
-
Define Value- Identify the added value your company brings to society. What makes you stand out from your competitors?
-
Reduce Waste – Eliminate all activities that don't add value throughout the supply chain.
-
Create Flow - Make sure work runs smoothly without interruptions.
-
Standardize and Simplify – Make processes as consistent, repeatable, and as simple as possible.
-
Build relationships - Develop and maintain personal relationships with both your internal and external stakeholders.
Although lean manufacturing has always been around, it is gaining popularity in recent years because of a renewed interest for the economy after 2008's global financial crisis. To increase their competitiveness, many businesses have turned to lean manufacturing. Some economists even believe that lean manufacturing can be a key factor in economic recovery.
Lean manufacturing is now becoming a common practice in the automotive industry, with many benefits. These include better customer satisfaction and lower inventory levels. They also result in lower operating costs.
The principles of lean manufacturing can be applied in almost any area of an organization. It is especially useful for the production aspect of an organization, as it ensures that every step in the value chain is efficient and effective.
There are three types principally of lean manufacturing:
-
Just-in Time Manufacturing, (JIT): This kind of lean manufacturing is also commonly known as "pull-systems." JIT is a process in which components can be assembled at the point they are needed, instead of being made ahead of time. This method reduces lead times, increases availability, and decreases inventory.
-
Zero Defects Manufacturing: ZDM ensures that no defective units leave the manufacturing plant. It is better to repair a part than have it removed from the production line if it needs to be fixed. This is also true for finished products that require minor repairs before shipping.
-
Continuous Improvement (CI),: Continuous improvement aims improve the efficiency and effectiveness of operations by continuously identifying issues and making changes to reduce waste. Continuous Improvement (CI) involves continuous improvement in processes, people, tools, and infrastructure.