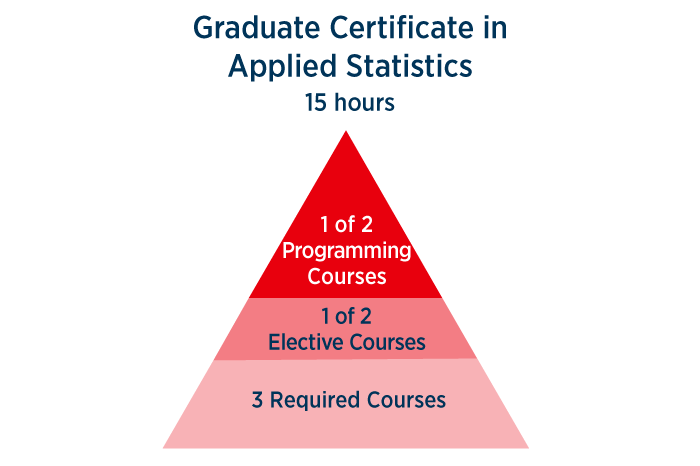
There are many types to choose from, but which one would be best for your company? Learn more about Continuous manufacturing, Process manufacturing and Job shop manufacturing. Each type of manufacturing has its advantages and disadvantages. This article will discuss the differences between these four types. Based on your industry, location and product type, you will be able to choose the right model for your business. Once you have chosen the best type for your business, you must consider sales, production, as well as quality control.
Discrete Manufacturing
Discrete manufacturing refers to a process where different products are made. These products include automobiles, toys, and aeroplanes. Discrete Manufacturing allows companies to focus more on their individual products than on mass production. In other words, discrete manufacture allows for the creation of unique parts in an aeroplane using multiple manufacturing processes. Discrete manufacturing is a popular way to manufacture high-tech items.
Discrete manufacturing produces distinct items. Instead of making many identical products, discrete production produces unique items that can be easily identified with serial numbers, labels and other numerical attributes. For example, a smartphone may consist of different parts manufactured in multiple factories in different states, and the individual parts are assembled only once the finished product is ready to be sold. The same is true for the smartphone's case. It could contain parts from different plants, such as the Missouri plant headquarters.
Process manufacturing
The idea of process manufacturing is a sub-field of manufacturing that includes formulas and recipes. Process manufacturing is different from discrete manufacturing which is focused on individual units, bills and assembly of components. These two types of manufacturing have very distinct goals. Each of these methods is important in the manufacturing process. These are three ways to distinguish between process and discrete manufacturing. Let's have a look at them all.
Batch process manufacturing is similar in many ways to continuous process manufacturing. However, it uses larger quantities and runs continuously. Batch process manufacturing is common in pharmaceuticals, paper production, newspaper printing, bookbinding, and some food products. This method is not suitable for all industries. It's often too complex and costly for smaller-scale businesses to use. This method is used by most companies when they need large quantities of the exact same product.
Job shop manufacturing
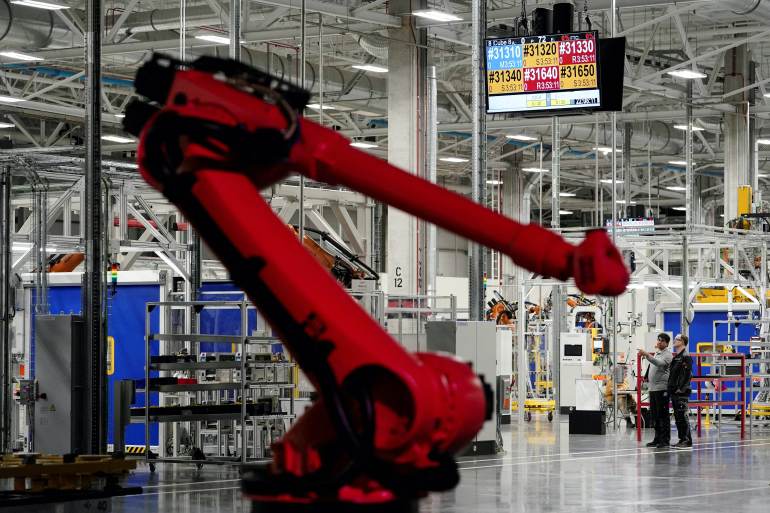
Job shop manufacturing is small-scale manufacturing that specializes in custom, semi-custom, and batch manufacturing. Once each job has been completed, job shops can move on. This method of production, also known as lean manufacture, is more efficient than any other. Here are some advantages of job shop production. You can read on to learn about this type of manufacturing. It might be a good option for your business if you need to manufacture products or services.
First, job shops need to be more efficient. Integrating new manufacturing methods is essential to achieve a lean manufacturing process. These principles are particularly relevant for high-volume operations and emphasize quality control and just in-time production. A job shop can improve productivity and reduce costs by adopting new manufacturing principles. Each job must be done one at a given time. There should not be any waiting.
Continuous manufacturing
Continuous manufacturing offers many benefits, including the flexibility of tracking. This is especially beneficial when it concerns product failure. Since the production line's time stamp and the raw material quantity can help identify when a batch has gone wrong, continuous manufacturing allows for more flexible tracking. The manufacturer can also reduce the risk of product shortages and waste by increasing their tracking. In the pharmaceutical industry, continuous manufacturing is also gaining popularity.
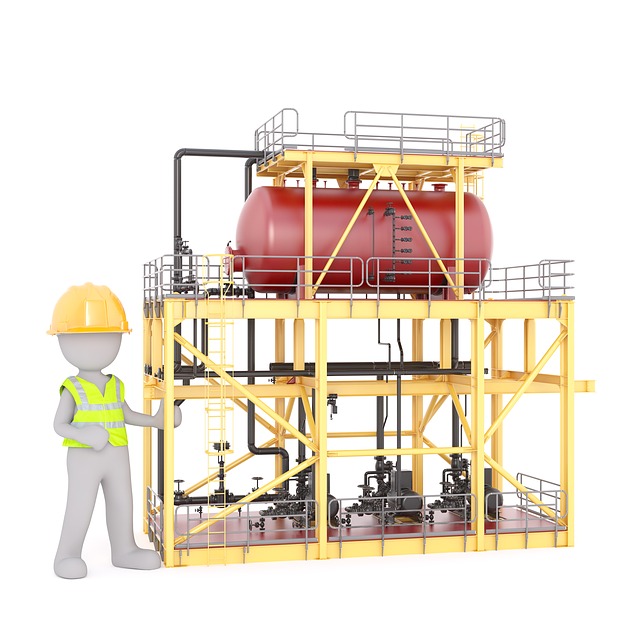
Despite the obvious benefits of continuous manufacturing, implementation can be slow. Implementation is often hampered by the fact that the process is not fully integrated with the rest of the company. Continuous manufacturing has the potential of being a game changer in the pharmaceutical business, despite the limitations. The process must be seamless and integrate with continuous flow and end to end integration for it to be effective. The pharmaceutical industry has long recognized the benefits of continuous manufacturing, but implementation has been slow.
FAQ
What are the responsibilities of a logistic manager?
Logistics managers ensure that goods arrive on time and are unharmed. This is accomplished by using the experience and knowledge gained from working with company products. He/she should also ensure enough stock is available to meet demand.
What are the 4 types manufacturing?
Manufacturing is the process of transforming raw materials into useful products using machines and processes. It includes many different activities like designing, building and testing, packaging, shipping and selling, as well as servicing.
How can I find out more about manufacturing?
Practical experience is the best way of learning about manufacturing. You can read books, or watch instructional videos if you don't have the opportunity to do so.
Why automate your factory?
Modern warehousing has seen automation take center stage. E-commerce has brought increased demand for more efficient and quicker delivery times.
Warehouses must be able to quickly adapt to changing demands. They must invest heavily in technology to do this. Automating warehouses is a great way to save money. Here are some reasons why it's worth investing in automation:
-
Increases throughput/productivity
-
Reduces errors
-
Increases accuracy
-
Boosts safety
-
Eliminates bottlenecks
-
Companies can scale more easily
-
Makes workers more efficient
-
The warehouse can be viewed from all angles.
-
Enhances customer experience
-
Improves employee satisfaction
-
It reduces downtime, and increases uptime
-
Ensures quality products are delivered on time
-
Eliminates human error
-
It helps ensure compliance with regulations
What jobs are available in logistics?
There are many kinds of jobs available within logistics. Here are some:
-
Warehouse workers – They load and unload pallets and trucks.
-
Transportation drivers – These drivers drive trucks and wagons to transport goods and pick up the goods.
-
Freight handlers: They sort and package freight in warehouses.
-
Inventory managers - They oversee the inventory of goods in warehouses.
-
Sales representatives - They sell products to customers.
-
Logistics coordinators - They plan and organize logistics operations.
-
Purchasing agents are those who purchase goods and services for the company.
-
Customer service representatives - They answer calls and emails from customers.
-
Shipping clerks: They process shipping requests and issue bills.
-
Order fillers are people who fill orders based only on what was ordered.
-
Quality control inspectors – They inspect incoming and outgoing products to ensure that there are no defects.
-
Others – There are many other types available in logistics. They include transport supervisors, cargo specialists and others.
Statistics
- According to the United Nations Industrial Development Organization (UNIDO), China is the top manufacturer worldwide by 2019 output, producing 28.7% of the total global manufacturing output, followed by the United States, Japan, Germany, and India.[52][53] (en.wikipedia.org)
- According to a Statista study, U.S. businesses spent $1.63 trillion on logistics in 2019, moving goods from origin to end user through various supply chain network segments. (netsuite.com)
- (2:04) MTO is a production technique wherein products are customized according to customer specifications, and production only starts after an order is received. (oracle.com)
- Many factories witnessed a 30% increase in output due to the shift to electric motors. (en.wikipedia.org)
- You can multiply the result by 100 to get the total percent of monthly overhead. (investopedia.com)
External Links
How To
Six Sigma in Manufacturing:
Six Sigma is defined as "the application of statistical process control (SPC) techniques to achieve continuous improvement." Motorola's Quality Improvement Department created Six Sigma at their Tokyo plant, Japan in 1986. Six Sigma's basic concept is to improve quality and eliminate defects through standardization. Since there are no perfect products, or services, this approach has been adopted by many companies over the years. Six Sigma's main objective is to reduce variations from the production average. You can calculate the percentage of deviation from the norm by taking a sample of your product and comparing it to the average. If there is a significant deviation from the norm, you will know that something needs to change.
Understanding the dynamics of variability within your business is the first step in Six Sigma. Once you understand that, it is time to identify the sources of variation. You'll also want to determine whether these variations are random or systematic. Random variations are caused by human errors. Systematic variations can be caused by outside factors. These are, for instance, random variations that occur when widgets are made and some fall off the production line. However, if you notice that every time you assemble a widget, it always falls apart at exactly the same place, then that would be a systematic problem.
Once you have identified the problem, you can design solutions. This could mean changing your approach or redesigning the entire process. After implementing the new changes, you should test them again to see if they worked. If they fail, you can go back to the drawing board to come up with a different plan.