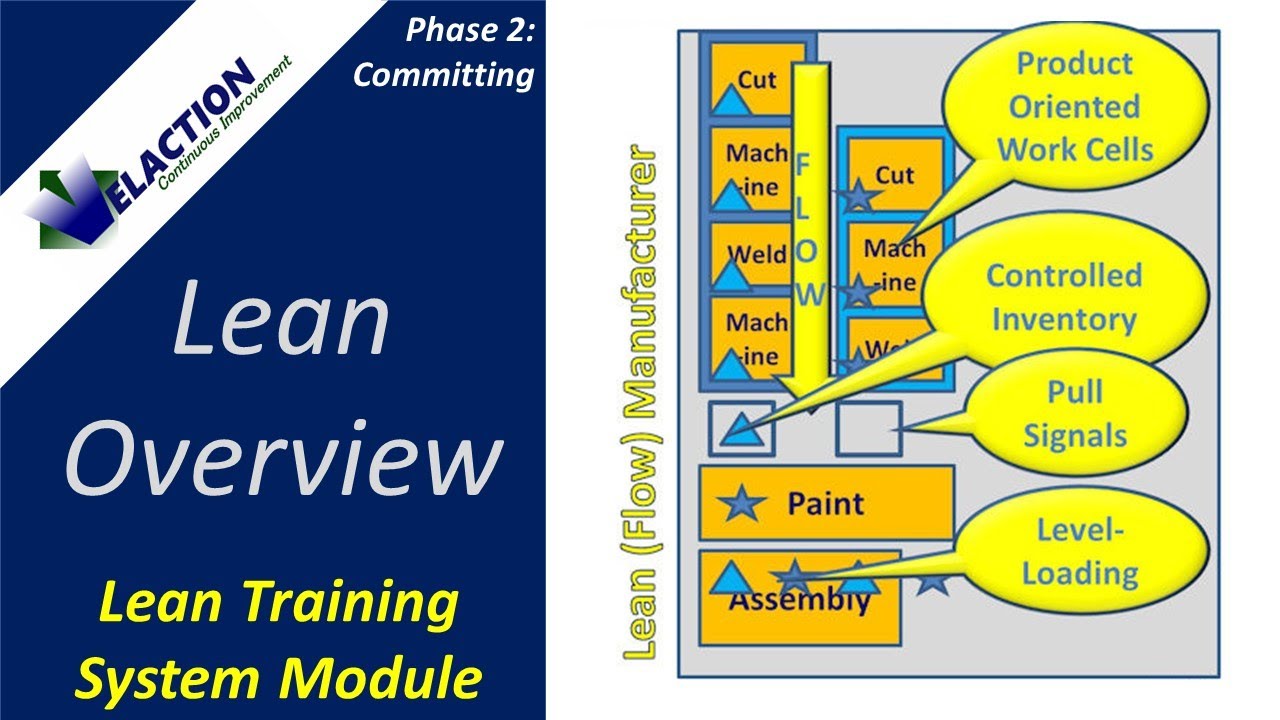
Industrial engineers are responsible for designing efficient systems that integrate people, machines, materials and information to create a product, or provide a particular service. They may work in an office or in a production setting, such as a manufacturing facility or warehouse.
Industrial Engineer Entry Level in Texas
You will be responsible for making sure that the production process runs smoothly. You'll be responsible to analyze problems, troubleshoot issues and implement changes in order to improve efficiency. You may also train and support technicians who use the systems and equipment you designed.
The duties you perform will vary depending on what type of business you work for, and their requirements. For example, some manufacturers need you to develop a process for handling hazardous waste. Some manufacturers require that you develop a method for controlling and monitoring the flow of raw material.
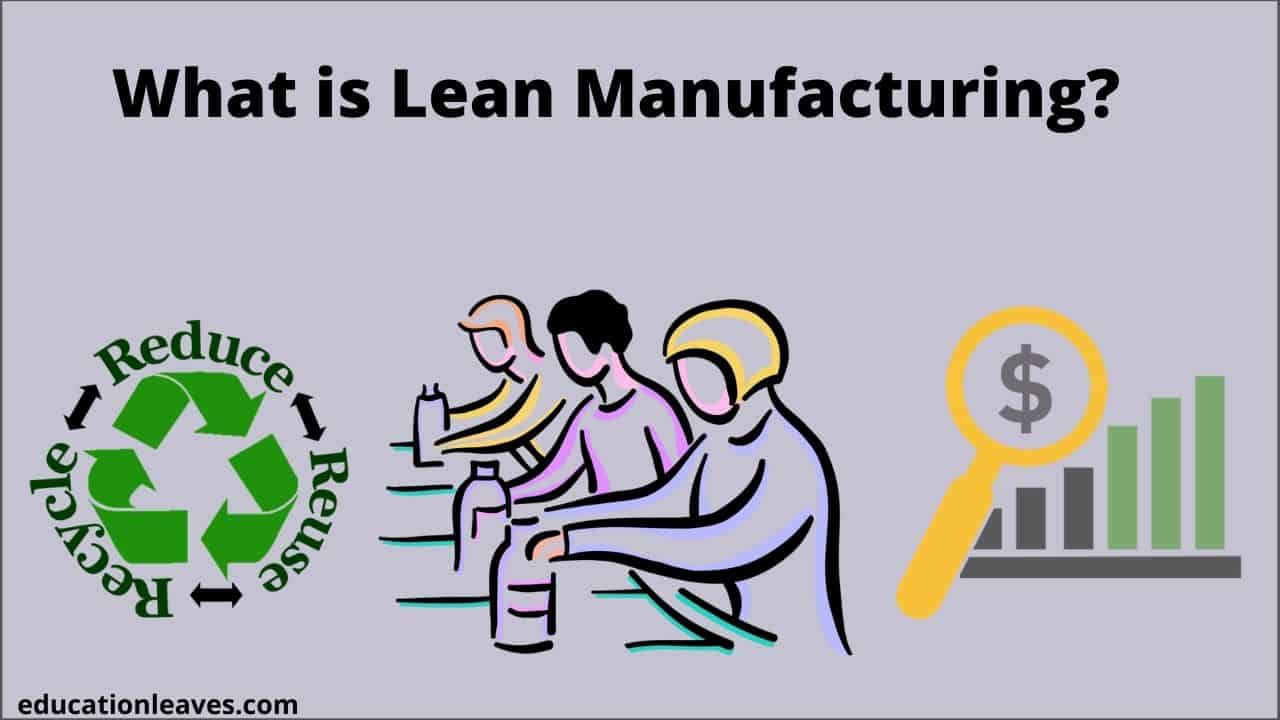
Manufacturers are always looking for ways to cut costs and increase efficiency, so you could find yourself working on projects to reduce waste in production processes. It could be reducing inventory, increasing the efficiency and effectiveness of machinery, or identifying wasteful practices.
You could work for a manufacturer of transportation equipment, or an electronics and computer firm. These are usually full-time jobs, and employment growth is expected to be 10% in the next decade.
Manufacturing Engineering Jobs in Texas
Start your career in industrial engineering by taking a job at a company that makes heavy machinery, or energy equipment. It is an excellent way to learn industrial engineering and many plant managers look for candidates with such experience.
During the time you spend at the plant, it is expected that you participate in various training programs and seminars. These training opportunities are designed to help you become more productive as a member of your team. You may be required to perform research or specialized tasks that will improve your skills and knowledge as an industrial engineering.
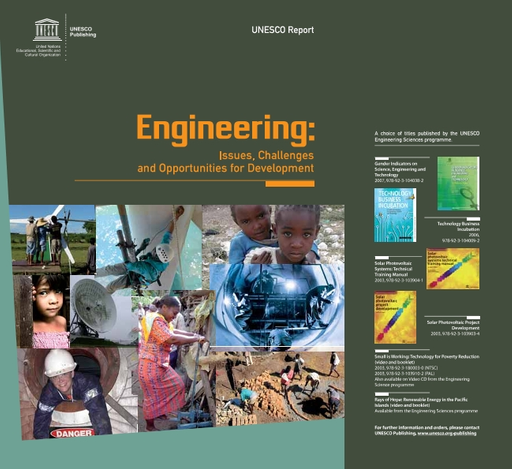
Eastman Company Manufacturing Engineer
If you have the right skills, Eastman Chemical could offer you a position as a industrial engineer in Mcallen. It is a rewarding, fast-paced role that allows you to work in a technology and energy company.
You will be an integral part of the industrial engineering team, responsible for implementing and maintaining engineered work standards in distribution centers throughout the country. You will play a vital role in the industrial engineering team. This includes presenting and providing engineering standards to employees at these facilities.
FAQ
What is the difference in Production Planning and Scheduling, you ask?
Production Planning (PP), also known as forecasting and identifying production capacities, is the process that determines what product needs to be produced at any particular time. This is done through forecasting demand and identifying production capacities.
Scheduling involves the assignment of dates and times to tasks in order to complete them within the timeframe.
How does a Production Planner differ from a Project Manager?
The difference between a product planner and project manager is that a planer is typically the one who organizes and plans the entire project. A production planner, however, is mostly involved in the planning stages.
How can we reduce manufacturing overproduction?
It is essential to find better ways to manage inventory to reduce overproduction. This would decrease the time that is spent on inefficient activities like purchasing, storing, or maintaining excess stock. This could help us free up our time for other productive tasks.
Kanban systems are one way to achieve this. A Kanbanboard is a visual tool that allows you to keep track of the work being done. A Kanban system allows work items to move through several states before reaching their final destination. Each state is assigned a different priority.
When work is completed, it can be transferred to the next stage. However, if a task is still at the beginning stages, it will remain so until it reaches the end of the process.
This helps to keep work moving forward while ensuring that no work is left behind. Managers can view the Kanban board to see how much work they have done. This allows them to adjust their workflows based on real-time information.
Lean manufacturing can also be used to reduce inventory levels. Lean manufacturing focuses on eliminating waste throughout the entire production chain. Waste includes anything that does not add value to the product. Here are some examples of common types.
-
Overproduction
-
Inventory
-
Unnecessary packaging
-
Excess materials
By implementing these ideas, manufacturers can improve efficiency and cut costs.
Are there ways to automate parts of manufacturing?
Yes! Yes. Automation has been around since ancient time. The Egyptians created the wheel thousands years ago. Nowadays, we use robots for assembly lines.
Actually, robotics can be used in manufacturing for many purposes. These include:
-
Robots for assembly line
-
Robot welding
-
Robot painting
-
Robotics inspection
-
Robots that make products
Automation could also be used to improve manufacturing. 3D printing makes it possible to produce custom products in a matter of days or weeks.
Statistics
- You can multiply the result by 100 to get the total percent of monthly overhead. (investopedia.com)
- In 2021, an estimated 12.1 million Americans work in the manufacturing sector.6 (investopedia.com)
- According to a Statista study, U.S. businesses spent $1.63 trillion on logistics in 2019, moving goods from origin to end user through various supply chain network segments. (netsuite.com)
- [54][55] These are the top 50 countries by the total value of manufacturing output in US dollars for its noted year according to World Bank.[56] (en.wikipedia.org)
- In the United States, for example, manufacturing makes up 15% of the economic output. (twi-global.com)
External Links
How To
How to Use Lean Manufacturing for the Production of Goods
Lean manufacturing refers to a method of managing that seeks to improve efficiency and decrease waste. It was created in Japan by Taiichi Ohno during the 1970s and 80s. He received the Toyota Production System award (TPS), from Kanji Toyoda, founder of TPS. Michael L. Watkins published the book "The Machine That Changed the World", which was the first to be published about lean manufacturing.
Lean manufacturing, often described as a set and practice of principles, is aimed at improving the quality, speed, cost, and efficiency of products, services, and other activities. It emphasizes the elimination of defects and waste throughout the value stream. Lean manufacturing is called just-in-time (JIT), zero defect, total productive maintenance (TPM), or 5S. Lean manufacturing seeks to eliminate non-value added activities, such as inspection, work, waiting, and rework.
Lean manufacturing can help companies improve their product quality and reduce costs. Additionally, it helps them achieve their goals more quickly and reduces employee turnover. Lean manufacturing is considered one of the most effective ways to manage the entire value chain, including suppliers, customers, distributors, retailers, and employees. Lean manufacturing practices are widespread in many industries. For example, Toyota's philosophy underpins its success in automobiles, electronics, appliances, healthcare, chemical engineering, aerospace, paper, food, etc.
Five fundamental principles underlie lean manufacturing.
-
Define Value - Determine the value that your business brings to society. Also, identify what sets you apart from your competitors.
-
Reduce Waste – Eliminate all activities that don't add value throughout the supply chain.
-
Create Flow - Ensure work moves smoothly through the process without interruption.
-
Standardize & simplify - Make processes consistent and repeatable.
-
Build Relationships- Develop personal relationships with both internal as well as external stakeholders.
Lean manufacturing, although not new, has seen renewed interest in the economic sector since 2008. To increase their competitiveness, many businesses have turned to lean manufacturing. Some economists even believe that lean manufacturing can be a key factor in economic recovery.
Lean manufacturing, which has many benefits, is now a standard practice in the automotive industry. These benefits include increased customer satisfaction, reduced inventory levels and lower operating costs.
It can be applied to any aspect of an organisation. However, it is particularly useful when applied to the production side of an organization because it ensures that all steps in the value chain are efficient and effective.
There are three types of lean manufacturing.
-
Just-in-Time Manufacturing (JIT): This type of lean manufacturing is commonly referred to as "pull systems." JIT refers to a system in which components are assembled at the point of use instead of being produced ahead of time. This approach is designed to reduce lead times and increase the availability of components. It also reduces inventory.
-
Zero Defects Manufacturing - ZDM: ZDM focuses its efforts on making sure that no defective units leave a manufacturing facility. If a part needs to be fixed during the assembly line, it should be repaired rather than scrapped. This is true even for finished products that only require minor repairs prior to shipping.
-
Continuous Improvement (CI), also known as Continuous Improvement, aims at improving the efficiency of operations through continuous identification and improvement to minimize or eliminate waste. Continuous Improvement involves continuous improvement of processes.