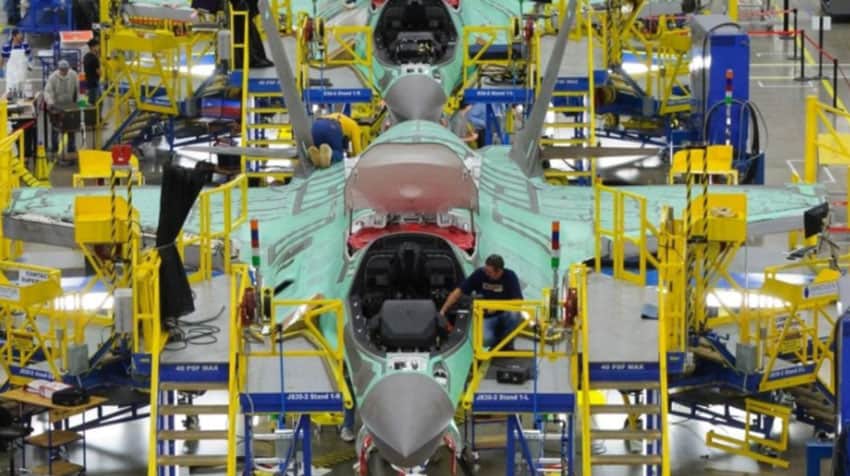
Supply Chain Management Review can be a useful resource for business owners who are looking for the most recent trends and developments in supply chain management. The magazine, which is based out of the U.S. since 2010, covers topics such as the role information technology plays in business and the changing natures of business models. This publication provides a comprehensive look at the industry and is particularly relevant for companies who manage large supply chains.
Manufacturing is the final stage in supply chain management
Supply chain management involves five elements. These are planning, sourcing raw material, manufacturing, delivery, and returns. Companies must be proficient in these areas to avoid costly bottlenecks. Because perishable goods are fragile, manufacturing is crucial.
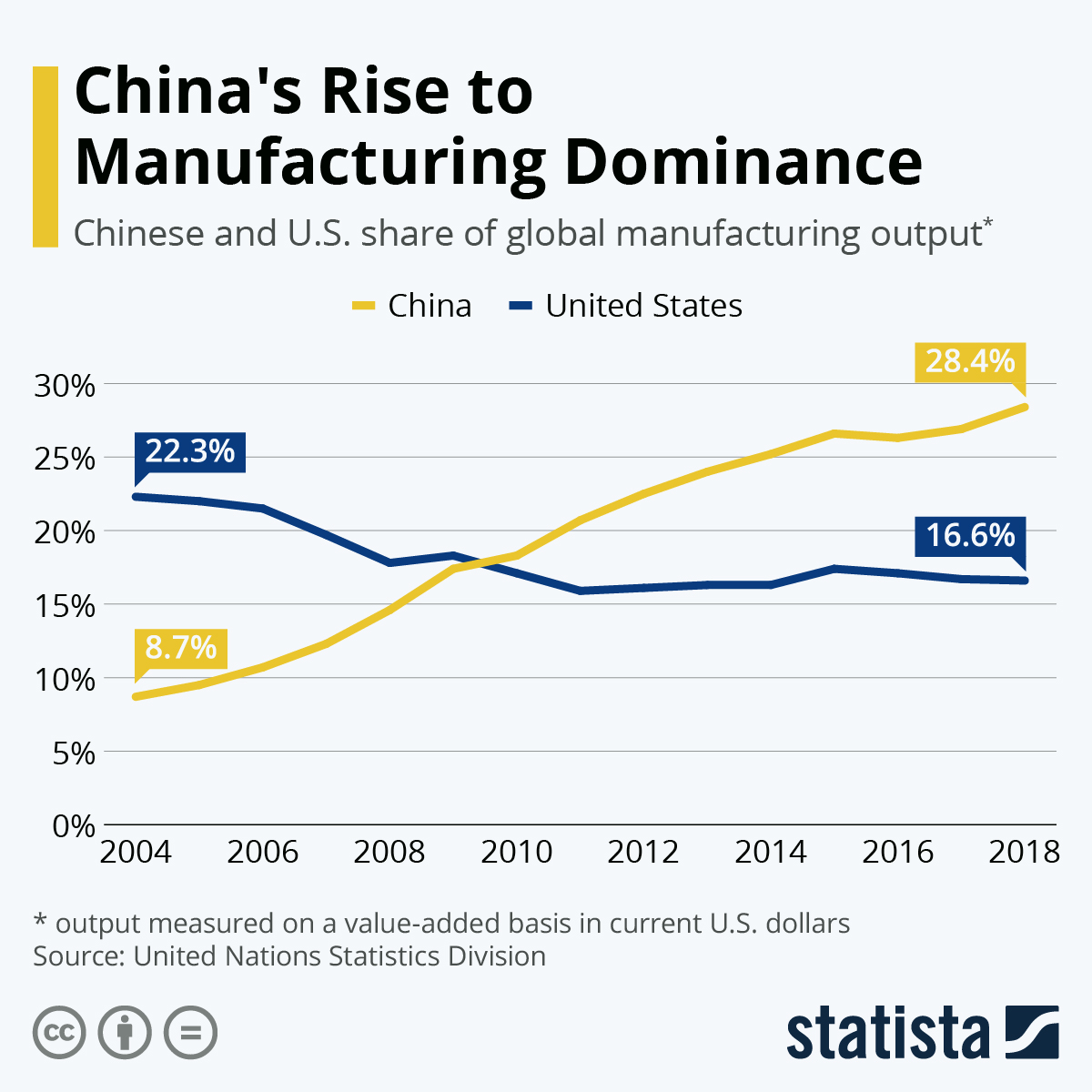
Reverse logistics
For a company to be successful in achieving its bottom line, reverse logistics management is crucial. This service allows companies use their existing infrastructure to lower costs and increase efficiency. This service can help improve a company's reputation by enabling them to adopt sustainable business practices. Reverse logistics comes with its own set of challenges.
Flexible model
Businesses can use a flexible supply network to meet customer demand when there is high and low demand. It relies on part segmentation, accurate stocking algorithms, and flexible planning, which includes incorporating automation on factory floors. Staples for writing utensils is one example. They anticipate a spike in demand during back to school season and stock up throughout the year.
Agile model
An Agile model of supply chain management review is a way for organizations to make significant changes and keep their supply chains responsive to change. While significant delays can result from changes such as the loss a manufacturing partner or logistical blocks, an agile supply chain can resolve these problems quickly. The model allows stakeholders in supply chains to see what is happening and can help them improve the efficiency of it. In addition, it allows organizations to outsource certain supply chain segments, resulting in lower costs. It can also be used to predict shortages and reduce stock inventories.
Model of fast-chain
The fast chain model is ideal for companies who frequently change product lines or compete for the same customers. This model is all about efficient inventory management and optimizing the use and productivity of production equipment. It's best suited to businesses that produce high-end items with short lives. In addition, this model also works well for businesses that need to get products to market quickly.
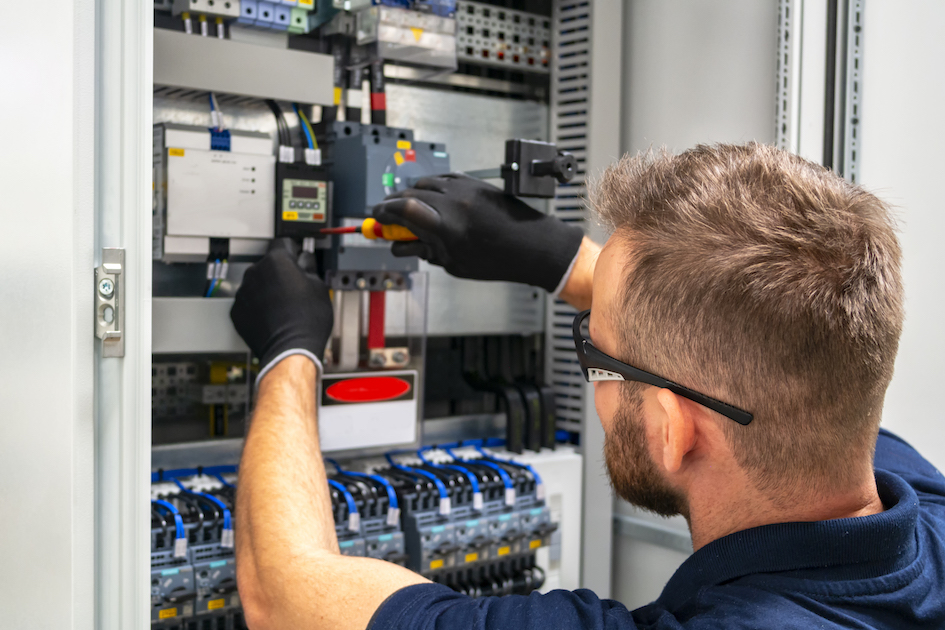
Supply chain management ethics
Companies should be mindful of ethics in supply-chain management, which has significant implications for their business performance as well as the bottom line. This issue is not limited to workers and factories. Supply chain companies also have to deal with environmental, social, or labor issues. To help ensure ethical supply chains, organizations are undertaking a number of initiatives.
FAQ
What is production planning?
Production Planning includes planning for all aspects related to production. This document will ensure everything is in order and ready to go when you need it. You should also have information to ensure the best possible results on set. It should include information about shooting locations, casting lists, crew details, equipment requirements, and shooting schedules.
It is important to first outline the type of film you would like to make. You may already know where you want the film to be shot, or perhaps you have specific locations and sets you wish to use. Once you have identified your locations and scenes it's time to begin figuring out what elements you will need for each one. One example is if you are unsure of the exact model you want but decide that you require a car. In this case, you could start looking up cars online to find out what models are available and then narrow your choices by choosing between different makes and models.
Once you have found the right car, you can start thinking about extras. Are you looking for people to sit in the front seats? Perhaps you have someone who needs to be able to walk around the back of your car. Perhaps you would like to change the interior colour from black to white. These questions will help to determine the style and feel of your car. Another thing you can do is think about what type of shots are desired. You will be filming close-ups and wide angles. Maybe you want the engine or the steering wheels to be shown. All of these things will help you identify the exact style of car you want to film.
Once you have determined all of the above, you can move on to creating a schedule. You will know when you should start and when you should finish shooting. Every day will have a time for you to arrive at the location, leave when you are leaving and return home when you are done. Everyone will know what they need and when. If you need to hire extra staff, you can make sure you book them in advance. There is no point in hiring someone who won't turn up because you didn't let him know.
Also, consider how many days you will be filming your schedule. Some projects only take one or two days, while others may last weeks. You should consider whether you will need more than one shot per week when creating your schedule. Multiplying takes in the same area will result both in increased costs and a longer time. It is better to be cautious and take fewer shots than you risk losing money if you are not sure if multiple takes are necessary.
Budgeting is another crucial aspect of production plan. You will be able to manage your resources if you have a realistic budget. Remember that you can always reduce the budget later on if you run into unforeseen problems. However, you shouldn't overestimate the amount of money you will spend. If you underestimate the cost of something, you will have less money left after paying for other items.
Production planning is a very detailed process, but once you understand how everything works together, it becomes easier to plan future projects.
What are the 4 types manufacturing?
Manufacturing is the process that transforms raw materials into useful products. It includes many different activities like designing, building and testing, packaging, shipping and selling, as well as servicing.
What are manufacturing & logistics?
Manufacturing is the process of creating goods from raw materials by using machines and processes. Logistics manages all aspects of the supply chain, including procurement, production planning and distribution, inventory control, transportation, customer service, and transport. As a broad term, manufacturing and logistics often refer to both the creation and delivery of products.
Is it possible to automate certain parts of manufacturing
Yes! Yes! Automation has existed since ancient times. The wheel was invented by the Egyptians thousands of years ago. Robots are now used to assist us in assembly lines.
There are many applications for robotics in manufacturing today. They include:
-
Robots for assembly line
-
Robot welding
-
Robot painting
-
Robotics inspection
-
Robots that make products
There are many other examples of how manufacturing could benefit from automation. 3D printing, for example, allows us to create custom products without waiting for them to be made.
How can we increase manufacturing efficiency?
First, we need to identify which factors are most critical in affecting production times. The next step is to identify the most important factors that affect production time. You can start by identifying the most important factors that impact production time. Once you have identified the factors, then try to find solutions.
What's the difference between Production Planning & Scheduling?
Production Planning (PP) is the process of determining what needs to be produced at any given point in time. Forecasting and identifying production capacity are two key elements to this process.
Scheduling refers the process by which tasks are assigned dates so that they can all be completed within the given timeframe.
What are the 7 Rs of logistics?
The acronym 7R's of Logistic is an acronym that stands for seven fundamental principles of logistics management. It was developed by the International Association of Business Logisticians (IABL) and published in 2004 as part of its "Seven Principles of Logistics Management" series.
The following letters make up the acronym:
-
Responsive - ensure all actions are legal and not harmful to others.
-
Reliable - Have confidence in your ability to fulfill all of your commitments.
-
Reasonable - use resources efficiently and don't waste them.
-
Realistic – consider all aspects of operations, from cost-effectiveness to environmental impact.
-
Respectful - treat people fairly and equitably.
-
Resourceful - look for opportunities to save money and increase productivity.
-
Recognizable: Provide customers with value-added service
Statistics
- Many factories witnessed a 30% increase in output due to the shift to electric motors. (en.wikipedia.org)
- You can multiply the result by 100 to get the total percent of monthly overhead. (investopedia.com)
- It's estimated that 10.8% of the U.S. GDP in 2020 was contributed to manufacturing. (investopedia.com)
- Job #1 is delivering the ordered product according to specifications: color, size, brand, and quantity. (netsuite.com)
- (2:04) MTO is a production technique wherein products are customized according to customer specifications, and production only starts after an order is received. (oracle.com)
External Links
How To
How to Use Just-In-Time Production
Just-intime (JIT), which is a method to minimize costs and maximize efficiency in business process, is one way. It's a way to ensure that you get the right resources at just the right time. This means that your only pay for the resources you actually use. The term was first coined by Frederick Taylor, who developed his theory while working as a foreman in the early 1900s. He observed how workers were paid overtime if there were delays in their work. He decided to ensure workers have enough time to do their jobs before starting work to improve productivity.
JIT is about planning ahead. You should have all the necessary resources ready to go so that you don’t waste money. Also, you should look at the whole project from start-to-finish and make sure you have the resources necessary to address any issues. If you anticipate that there might be problems, you'll have enough people and equipment to fix them. This will prevent you from spending extra money on unnecessary things.
There are several types of JIT techniques:
-
Demand-driven: This JIT is where you place regular orders for the parts/materials that are needed for your project. This will enable you to keep track of how much material is left after you use it. This will allow you to calculate how long it will take to make more.
-
Inventory-based: You stock materials in advance to make your projects easier. This allows for you to anticipate how much you can sell.
-
Project-driven: This means that you have enough money to pay for your project. When you know how much you need, you'll purchase the appropriate amount of materials.
-
Resource-based JIT: This is the most popular form of JIT. Here, you allocate certain resources based on demand. For example, if there is a lot of work coming in, you will have more people assigned to them. If you don't have many orders, you'll assign fewer people to handle the workload.
-
Cost-based: This is similar to resource-based, except that here you're not just concerned about how many people you have but how much each person costs.
-
Price-based: This is very similar to cost-based, except that instead of looking at how much each individual worker costs, you look at the overall price of the company.
-
Material-based is an alternative to cost-based. Instead of looking at the total cost in the company, this method focuses on the average amount of raw materials that you consume.
-
Time-based: Another variation of resource-based JIT. Instead of focusing solely on the amount each employee costs, focus on how long it takes for the project to be completed.
-
Quality-based JIT: Another variation on resource-based JIT. Instead of focusing on the cost of each worker or how long it takes, think about how high quality your product is.
-
Value-based JIT: One of the most recent forms of JIT. In this case, you're not concerned with how well the products perform or whether they meet customer expectations. Instead, you are focused on adding value to the marketplace.
-
Stock-based. This method is inventory-based and focuses only on the actual production at any given point. It's useful when you want maximum production and minimal inventory.
-
Just-intime (JIT), planning is a combination JIT management and supply chain management. It's the process of scheduling delivery of components immediately after they are ordered. This is important as it reduces lead time and increases throughput.