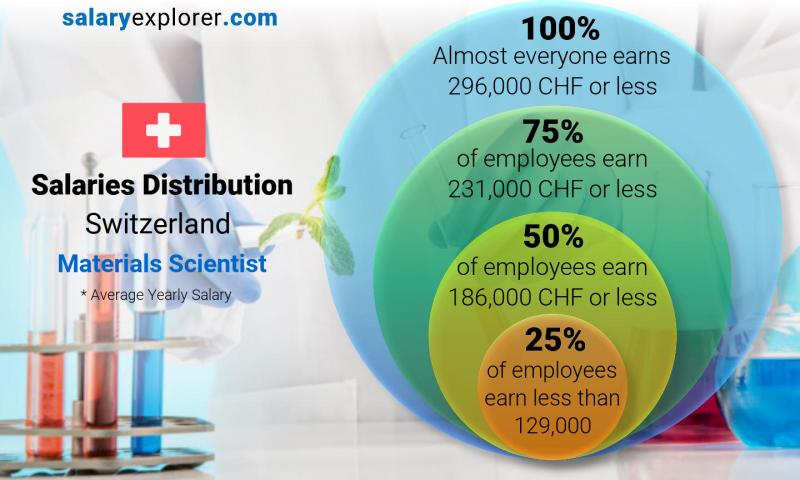
A director of manufacturing is responsible for managing the production process for a company. They are responsible for overseeing all aspects of manufacturing, from design through to production. To succeed in this role, the ideal candidate must have extensive experience in manufacturing and be familiar with new technologies. Examples of such technologies are robotics and 3-D printing. The director who is up-to-date with these technologies will be a valuable asset to the company. As the manufacturing industry evolves, the director's job will be more complex. He or she will have to coordinate with both the engineering and operations departments.
Salary for a director in manufacturing
A Director of Manufacturing's salary can vary greatly, depending on the region they work in. Many directors earn in the six-figures range. Some directors make significantly more than others. Based on years of education and experience, the salary of a Director in Manufacturing can also vary. In order to determine how much you'll earn in your area, consider a few factors that may influence your salary:
The salary for a Director Of Manufacturing varies, but in general, the more experience you have, the higher your salary will be. Like many other positions, salary can be affected by the cost of living or where you live. While you may earn more if your location is a major city, it's possible to make a living in that area. It is important that you are always willing to negotiate a higher salary when the opportunity arises.
The annual salary of a Director of Manufacturing Operations is between $181,500 to $66,000. The salary of a Director Manufacturing Operations is highly variable. It can vary by up 8% among different cities. Fremont's director manufacturing operations can expect to earn $128.493 to $164.500. This makes Fremont, CA a significantly better place than the national average. However, salaries for Director of Manufacturing Operations vary depending on location, experience, and company.
Education required
The director for manufacturing is responsible in managing a manufacturing plant and supervising the production process. This job includes managing new employees, quality assurance, working with designers and meeting production standards. A director in manufacturing typically reports directly to the senior management team. This person executes policies and sales initiatives. Candidates should have some experience in manufacturing and be good communicators. There are different educational requirements to become a director in manufacturing.
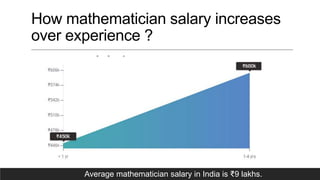
While a degree in engineering is not required for director-level manufacturing jobs, it will help you to build your knowledge and skills. A MBA in industrial management or business administration would be a great option for this job. It teaches candidates about economics, management, and organizational behavior. You will ultimately be responsible for managing diverse groups of people.
As a director in manufacturing you will work closely alongside engineers and designers during the product design phase. You will play a key role in this stage by evaluating new processes and making sure quality standards are met before you commit resources to larger productions. In addition to overseeing the production process, successful directors serve as coaches for employees. They will coach them in best practices and risk mitigation. They will also mentor them on best practices and risk mitigation.
Experience required
For this position, a bachelor's Degree in a relevant subject and 5-10 years of progressive experience are usually required. For this position, manufacturing companies prefer to recruit internal employees. The ideal candidate should have a solid understanding of the manufacturing process as well as business objectives. However, a graduate degree may also be desired by some employers. Additional training may be required for candidates in their chosen field.
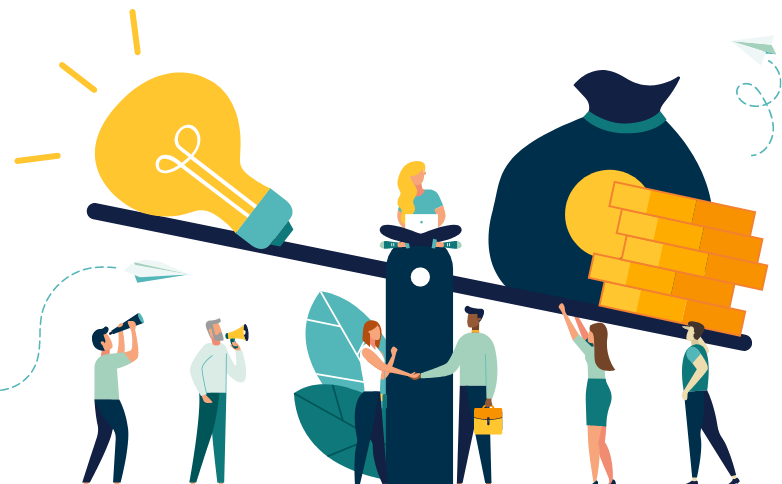
The production process is overseen by a director of manufacturing, which includes engineers, supervisors, workers, and other personnel. They may be responsible in solving problems and creating solutions. A director of manufacturing may not only oversee production but also develop and implement quality-control programs. Directly reporting to the head of manufacturing, a director of manufacturing is responsible for developing and implementing quality-control programs. Manufacturing experience is a must. Experience in manufacturing management can help you succeed in this position.
Experience as a manufacturing director essential. Directors should have at least 10 years' experience in a manufacturing setting. These people might have been employed as technicians or supervisors in manufacturing. They must also be able to communicate well. Also, a director of manufacturing needs to have a good understanding of business strategy. Finally, a director of manufacturing must be able to work effectively with other departments within the organization. As such, the director is responsible for overseeing the production process and ensuring that it meets all quality standards.
FAQ
Why should you automate your warehouse?
Modern warehouses have become more dependent on automation. Increased demand for efficient and faster delivery has resulted in a rise in e-commerce.
Warehouses need to adapt quickly to meet changing needs. To do so, they must invest heavily in technology. Automation warehouses can bring many benefits. Here are some of the reasons automation is worth your investment:
-
Increases throughput/productivity
-
Reduces errors
-
Increases accuracy
-
Safety increases
-
Eliminates bottlenecks
-
Allows companies scale more easily
-
This makes workers more productive
-
The warehouse can be viewed from all angles.
-
Enhances customer experience
-
Improves employee satisfaction
-
Minimizes downtime and increases uptime
-
High quality products delivered on-time
-
Removing human error
-
This helps to ensure compliance with regulations
Is automation necessary in manufacturing?
Automation is important not only for manufacturers but also for service providers. It allows them to offer services faster and more efficiently. They can also reduce their costs by reducing human error and improving productivity.
Can certain manufacturing steps be automated?
Yes! Since ancient times, automation has been in existence. The Egyptians created the wheel thousands years ago. Nowadays, we use robots for assembly lines.
There are many uses of robotics today in manufacturing. These include:
-
Assembly line robots
-
Robot welding
-
Robot painting
-
Robotics inspection
-
Robots that make products
Manufacturing could also benefit from automation in other ways. 3D printing makes it possible to produce custom products in a matter of days or weeks.
What is production management?
Production Planning is the creation of a plan to cover all aspects, such as scheduling, budgeting. Location, crew, equipment, props and other details. This document ensures that everything is prepared and available when you are ready for shooting. This document should also include information on how to get the best result on set. This includes location information, crew details, equipment specifications, and casting lists.
The first step is to outline what you want to film. You might have an idea of where you want to film, or you may have specific locations or sets in mind. Once you have determined your scenes and locations, it is time to start figuring out the elements that you will need for each scene. One example is if you are unsure of the exact model you want but decide that you require a car. If this is the case, you might start searching online for car models and then narrow your options by selecting from different makes.
Once you have found the right car, you can start thinking about extras. Do you have people who need to be seated in the front seat? You might also need someone to help you get around the back. Maybe you'd like to change the interior from black to a white color. These questions will help determine the look and feel you want for your car. The type of shots that you are looking for is another thing to consider. Are you going to be shooting close-ups? Or wide angles? Maybe you want to show your engine or the steering wheel. These factors will help you determine which car style you want to film.
Once you have established all the details, you can create a schedule. You can create a schedule that will outline when you must start and finish your shoots. Every day will have a time for you to arrive at the location, leave when you are leaving and return home when you are done. Everyone will know what they need and when. If you need to hire extra staff, you can make sure you book them in advance. There is no point in hiring someone who won't turn up because you didn't let him know.
You will need to factor in the days that you have to film when creating your schedule. Some projects take only a few days while others can last several weeks. When creating your schedule, be aware of whether you need more shots per day. Multiplying takes in the same area will result both in increased costs and a longer time. You can't be certain if you will need multiple takes so it is better not to shoot too many.
Budgeting is another important aspect of production planning. You will be able to manage your resources if you have a realistic budget. If you have to reduce your budget due to unexpected circumstances, you can always lower it later. But, don't underestimate how much money you'll spend. If you underestimate the cost of something, you will have less money left after paying for other items.
Planning production is a tedious process. Once you have a good understanding of how everything works together, planning future projects becomes easy.
Statistics
- According to a Statista study, U.S. businesses spent $1.63 trillion on logistics in 2019, moving goods from origin to end user through various supply chain network segments. (netsuite.com)
- [54][55] These are the top 50 countries by the total value of manufacturing output in US dollars for its noted year according to World Bank.[56] (en.wikipedia.org)
- In 2021, an estimated 12.1 million Americans work in the manufacturing sector.6 (investopedia.com)
- Many factories witnessed a 30% increase in output due to the shift to electric motors. (en.wikipedia.org)
- (2:04) MTO is a production technique wherein products are customized according to customer specifications, and production only starts after an order is received. (oracle.com)
External Links
How To
Six Sigma in Manufacturing:
Six Sigma is defined by "the application SPC (statistical process control) techniques to achieve continuous improvements." Motorola's Quality Improvement Department developed it at their Tokyo plant in Japan in 1986. Six Sigma's main goal is to improve process quality by standardizing processes and eliminating defects. Since there are no perfect products, or services, this approach has been adopted by many companies over the years. The main goal of Six Sigma is to reduce variation from the mean value of production. It is possible to measure the performance of your product against an average and find the percentage of time that it differs from the norm. If you notice a large deviation, then it is time to fix it.
The first step toward implementing Six Sigma is understanding how variability works in your business. Once you understand this, you can then identify the causes of variation. These variations can also be classified as random or systematic. Random variations are caused by human errors. Systematic variations can be caused by outside factors. These are, for instance, random variations that occur when widgets are made and some fall off the production line. If however, you notice that each time you assemble a widget it falls apart in exactly the same spot, that is a problem.
After identifying the problem areas, you will need to devise solutions. This could mean changing your approach or redesigning the entire process. After implementing the new changes, you should test them again to see if they worked. If they didn't work, then you'll need to go back to the drawing board and come up with another plan.